Le digital au coeur de la révolution industrielle
La révolution industrielle 4.0 a apporté avec elle une multitude de changements qui ont eu un impact sur la manière dont les entreprises produisent et gèrent leurs opérations.
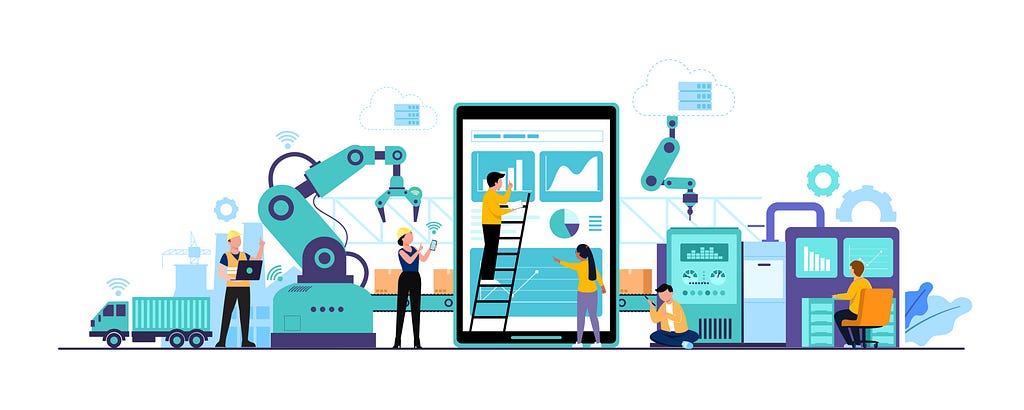
Digitalisation des mesures et traitement des non-conformités
Avec l’avènement du numérique, les entreprises ont de plus en plus recours à la digitalisation des mesures et du traitement des non-conformités, à l’évaluation et l’amélioration des pratiques industrielles afin d’optimiser leur efficacité et leur rentabilité.
La digitalisation des mesures consiste à remplacer les méthodes traditionnelles de définition des gammes de mesures et de recueil de données manuelles par des systèmes numériques. Cela permet aux entreprises de collecter des données plus rapidement et plus précisément, et de disposer d’informations plus détaillées, avec une meilleure traçabilité et accessibilité de l’information, sur les produits et la performance. Les capacités d’analyse d’écarts et de leurs évolutions sont également simplifiées et plus puissantes.
Le traitement des non-conformités est une autre pratique importante de la révolution industrielle 4.0. Avec l’utilisation de technologies de suivi et de surveillance en temps réel, les entreprises peuvent détecter rapidement les non-conformités dans leur processus de production ou de gestion. Cela permet aux entreprises de minimiser les perturbations et coûts, de prendre rapidement des mesures pour résoudre les problèmes et d’améliorer leur qualité de production et donc d’optimiser les coûts de production.
Cela favorise la qualité des produits en minimisant les non-conformités et en détectant rapidement les problèmes de production. Cela permet d’améliorer la rentabilité en optimisant l’efficacité des processus et en réduisant les temps d’arrêt de production. Enfin, cela permet d’améliorer la sécurité en réduisant les risques de blessures et d’accidents.
Evaluer améliorer et optimiser les processus industriels
L’évaluation des pratiques industrielles et connexes (QHSE, RSE, Lean,…) est un processus qui permet aux entreprises de déterminer l’efficacité de leurs méthodes de production et de gestion. Cela permet aux entreprises de détecter rapidement les inefficacités et les goulots d’étranglement, de les résoudre rapidement et d’optimiser la productivité.
Gérer les actifs de production
La gestion des actifs industriels a connu une évolution significative avec l’arrivée de l’industrie 4.0.
Les avancées technologiques et la digitalisation permettent aux entreprises de mettre en place :
- Un suivi de parc et de leur cycle de vie : vérifications, dont Vérifications Générales Périodiques (VGP), opérations de maintenance, partage de documentation,…
- Des systèmes de maintenance proactifs voir prédictifs,
- Une surveillance des performances de leurs équipements en temps réel; grâce à l’internet des objets (IoT) et à l’analyse de données, les responsables de la maintenance peuvent suivre les indicateurs clés de performance (KPI) et identifier les problèmes potentiels avant qu’ils ne se produisent.
Ces approches favorisent la réduction des temps d’arrêt imprévus, l’augmentation de la disponibilité des équipements et l’optimisation des coûts de maintenance. De plus, la gestion des actifs industriels s’intègre désormais dans une approche globale d’optimisation des flux de production et de maximisation de l’efficacité des équipements tout au long de leur cycle de vie.
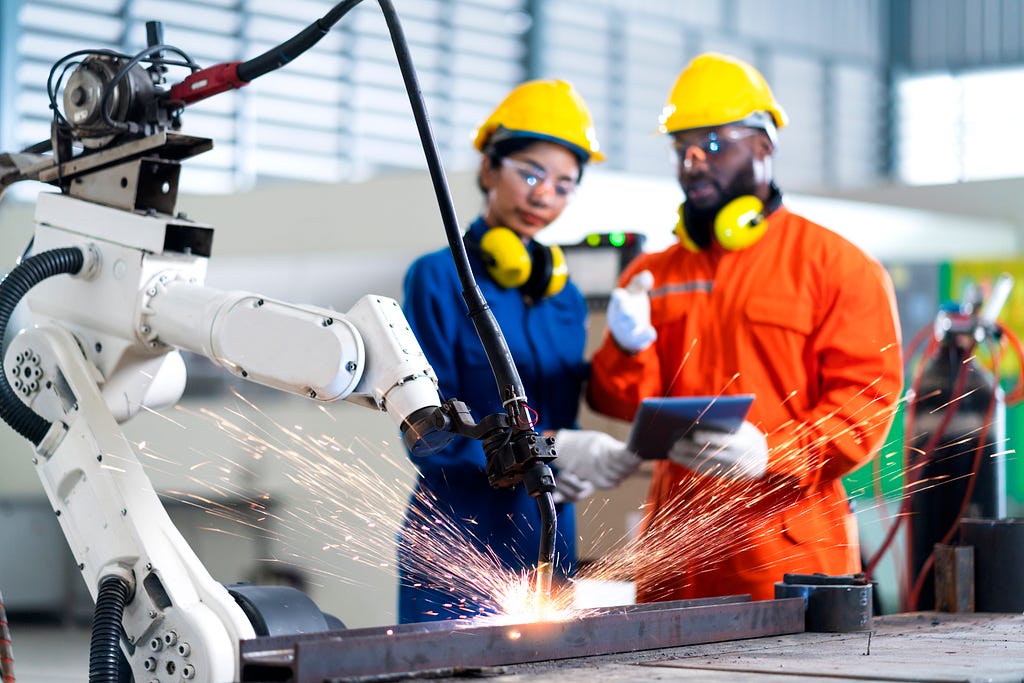
Conclusion
En somme, la révolution industrielle 4.0 a permis aux entreprises de tirer parti des technologies numériques pour améliorer leur efficacité et leur rentabilité.
L’évaluation des pratiques, la digitalisation des mesures et du traitement des non-conformités ainsi que de la gestion des parcs d’actifs, sont des éléments clés de cette révolution et peut aider les entreprises à atteindre leurs objectifs de manière plus efficace.