Maximiser l'efficacité opérationnelle grâce au Lean Manufacturing
L’efficacité opérationnelle et la compétitivité associée sont des enjeux centraux dans l’industrie moderne. Pour atteindre cet objectif, de nombreuses entreprises se tournent vers le Lean Manufacturing. Cette méthodologie, initiée par Toyota dans les années 1950, vise à maximiser la valeur tout en minimisant le gaspillage.
Dans cet article, nous explorerons les principes du Lean Manufacturing, sa mise en œuvre et les avantages qu’il offre aux entreprises. Plongeons dans cet univers où l’efficacité devient une seconde nature et où l’amélioration continue est la clé du succès.
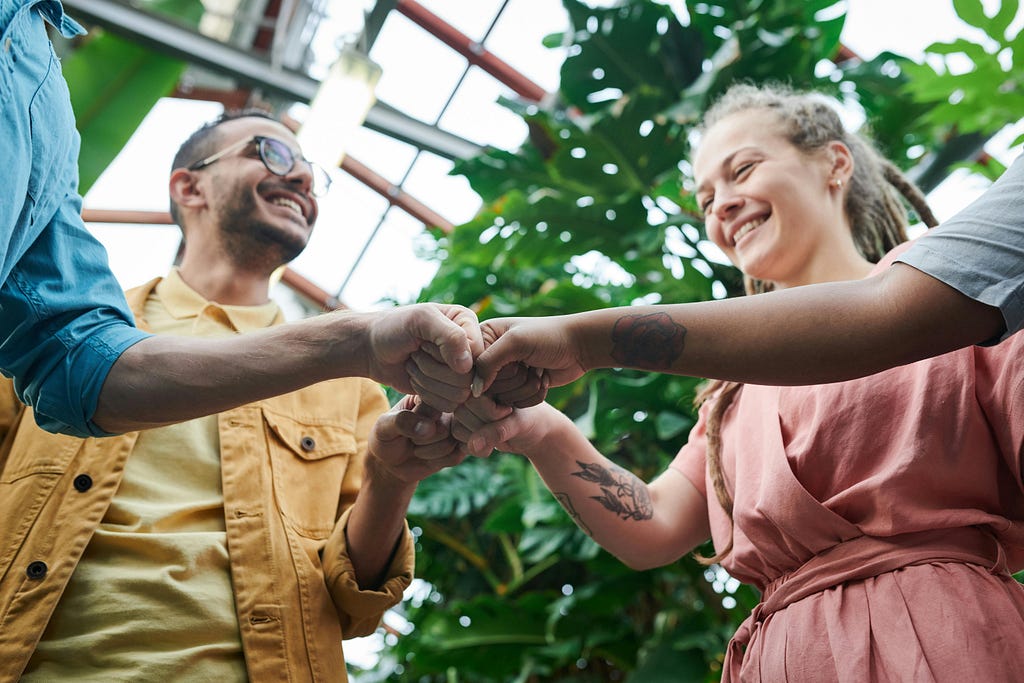
Qu’est-ce que le Lean Manufacturing ?
Le Lean Manufacturing, également connu sous le nom de Lean Production ou simplement Lean, est une méthodologie de gestion des processus de production qui vise à maximiser la valeur pour le client tout en minimisant le gaspillage. Le Lean repose sur des principes fondamentaux qui visent à rationaliser les opérations et à créer un environnement de travail plus efficace et productif.
Définition du Lean Manufacturing : Le Lean Manufacturing peut être défini comme un système de gestion qui se concentre sur la création de valeur tout en réduisant les gaspillages (muda en japonais) dans les processus de production. Il repose sur des principes tels que la minimisation des stocks, l’optimisation des flux de travail et l’amélioration continue.
Origines et historique du Lean : Le Lean Manufacturing trouve ses origines dans les pratiques de production mises en œuvre par Toyota après la Seconde Guerre mondiale. Inspiré par les méthodes de production de Ford, mais cherchant à éviter les inefficacités associées à la surproduction et aux stocks excessifs, Toyota a développé le système de production Toyota, qui est devenu la pierre angulaire du Lean Manufacturing.
Principes fondamentaux du Lean : Le Lean repose sur plusieurs principes fondamentaux, dont les plus importants sont :
- Élimination des gaspillages : Le Lean vise à identifier et à éliminer tout ce qui ne crée pas de valeur pour le client, y compris les stocks excessifs, les mouvements inutiles et les défauts de production.
- Création de valeur : Le Lean se concentre sur la création de valeur pour le client en fournissant des produits et des services de qualité, dans les délais et au meilleur coût possible.
- Flux continu : Le Lean encourage la mise en place de flux de production continus et fluides, sans interruptions ni temps d’attente inutiles.
- Engagement des employés : Les employés sont encouragés à contribuer activement à l’amélioration des processus et à participer à la résolution des problèmes grâce à la culture du Kaizen (amélioration continue).
Les principaux concepts du Lean Manufacturing
Le Lean Manufacturing repose sur plusieurs concepts clés qui jouent un rôle crucial dans l’optimisation des processus de production. Voici quelques-uns des concepts les plus importants :
Juste-à-temps (JIT) : Le Juste-à-temps est un concept qui vise à produire exactement ce dont le client a besoin, au moment où il en a besoin, et en quantité requise. Cela permet de réduire les coûts liés aux stocks et aux stocks excédentaires, tout en améliorant la réactivité de l’entreprise aux demandes du marché.
Kaizen : Le Kaizen, ou amélioration continue, est au cœur du Lean Manufacturing. Il s’agit d’une philosophie qui encourage tous les membres de l’organisation à rechercher en permanence des moyens d’améliorer les processus et les pratiques de travail. Le Kaizen repose sur l’idée que de petites améliorations constantes peuvent conduire à des gains significatifs en termes d’efficacité et de qualité.
Kanban : Le Kanban est un système de gestion des flux de production basé sur des signaux visuels. Il permet de contrôler le flux de travail en régulant la quantité de travail en cours et en évitant la surcharge des ressources. Le système Kanban est souvent utilisé pour minimiser les stocks et réduire les temps d’attente entre les étapes du processus de production.
Poka-Yoke : Le Poka-Yoke, ou conception d’erreur-proofing, consiste à concevoir des processus et des systèmes de manière à éviter les erreurs humaines ou les défauts de production. Cela peut inclure l’utilisation de dispositifs de sécurité, de guides visuels ou de contrôles automatisés pour détecter et corriger les erreurs avant qu’elles ne deviennent des problèmes majeurs.
5S : Les 5S sont une méthode d’organisation de l’espace de travail qui vise à optimiser l’efficacité et la sécurité. Les 5S se réfèrent à cinq étapes : trier, ranger, nettoyer, standardiser et maintenir en ordre. En mettant en œuvre les 5S, les entreprises peuvent améliorer la productivité, réduire les temps de recherche et créer un environnement de travail plus sûr et plus agréable.
Ces concepts ne sont que quelques-uns des nombreux outils et techniques utilisés dans le cadre du Lean Manufacturing. Dans la section suivante, nous explorerons la mise en œuvre pratique du Lean dans une organisation, ainsi que les étapes à suivre pour obtenir des résultats tangibles.
Mise en œuvre du Lean Manufacturing
La mise en œuvre du Lean Manufacturing dans une organisation nécessite un engagement total de la direction ainsi qu’une approche méthodique pour transformer les processus de production. Voici les étapes clés à suivre pour déployer avec succès le Lean Manufacturing :
Évaluation initiale : Avant de commencer, il est essentiel de réaliser une évaluation approfondie des processus existants pour identifier les sources de gaspillage et les domaines à améliorer. Cela peut impliquer des analyses de flux de valeur, des observations sur le terrain et des discussions avec les employés de tous les niveaux. Pour celà, campagnes et gemba walks E Value it s’avèrent précieux.
Formation du personnel : Une fois les domaines d’amélioration identifiés, il est important de fournir une formation adéquate à tous les niveaux de l’organisation. Cela peut inclure une formation sur les principes du Lean, ainsi que sur des outils spécifiques tels que le Kaizen, le 5S et le Kanban.
Planification et mise en œuvre des changements : Une fois que le personnel est formé, il est temps de commencer à mettre en œuvre les changements. Cela peut inclure la redéfinition des processus, la réorganisation de l’espace de travail et l’introduction de nouveaux systèmes de gestion des flux de production. Vous pouvez vous appuyer sur les Kanbans et la gestion de projets d’E Value it.
Surveillance et ajustement : Une fois que les changements ont été mis en place, il est important de surveiller régulièrement les résultats et de procéder aux ajustements nécessaires. Cela peut impliquer la collecte de données sur les performances, la tenue de réunions régulières d’amélioration et la prise en compte des commentaires des employés. Des gemba walks et AIC réguliers peuvent aider.
Culture d’amélioration continue : Enfin, pour que le Lean Manufacturing soit pleinement efficace, il est essentiel de créer une culture d’amélioration continue au sein de l’organisation. Cela implique de valoriser les idées et les contributions de tous les membres de l’équipe, et de favoriser un environnement où il est sûr de remettre en question les pratiques existantes et de proposer de nouvelles idées.
Avantages et bénéfices du Lean Manufacturing
Le Lean Manufacturing offre de nombreux avantages et bénéfices aux entreprises qui choisissent de l’adopter. Voici quelques-uns des principaux avantages :
Réduction des coûts de production : En éliminant les gaspillages et en optimisant les processus, le Lean Manufacturing permet de réduire les coûts liés à la surproduction, aux stocks excédentaires et aux retouches. Cela se traduit par des économies significatives sur le long terme.
Amélioration de la qualité des produits : En mettant l’accent sur la détection et la résolution des problèmes à la source, le Lean Manufacturing contribue à améliorer la qualité des produits en réduisant les défauts et les rebuts. Cela permet d’augmenter la satisfaction des clients et de renforcer la réputation de l’entreprise sur le marché.
Augmentation de la productivité et de la rentabilité : En optimisant les processus et en réduisant les temps d’arrêt et les temps d’attente, le Lean Manufacturing permet d’augmenter la productivité de l’entreprise. Cela se traduit par une utilisation plus efficace des ressources et une augmentation de la rentabilité globale.
Renforcement de la compétitivité sur le marché : En offrant des produits de meilleure qualité, à des prix compétitifs et avec des délais plus courts, le Lean Manufacturing permet aux entreprises de renforcer leur position concurrentielle sur le marché. Cela peut conduire à une croissance des parts de marché et à une expansion des activités.
En adoptant une approche systématique et axée sur l’amélioration continue, les entreprises peuvent réaliser des gains significatifs en termes d’efficacité opérationnelle, de qualité des produits et de satisfaction des clients grâce au Lean Manufacturing.
Limites du Lean Manufacturing
Bien que le Lean Manufacturing offre de nombreux avantages, il présente également quelques limites et défis à prendre en compte :
Complexité de mise en œuvre : La mise en œuvre réussie du Lean Manufacturing nécessite un engagement total de la direction ainsi qu’une approche méthodique pour transformer les processus de production. Cela peut être un processus long et complexe, en particulier dans les grandes organisations où il peut parfois être difficile de changer les mentalités et les pratiques établies.
Rigidité dans certains environnements : Dans certains environnements de production où la variabilité est élevée ou les demandes des clients sont imprévisibles, le Lean Manufacturing peut être perçu comme trop rigide pour s’adapter efficacement aux changements. Cela peut entraîner des problèmes de flexibilité et de réactivité aux demandes du marché.
Dépendance aux fournisseurs : Le Lean Manufacturing repose sur des chaînes d’approvisionnement efficaces et fiables. Cependant, cela signifie également que les entreprises peuvent devenir dépendantes de leurs fournisseurs pour fournir des matériaux et des composants de haute qualité, ce qui peut présenter des risques en cas de perturbations dans la chaîne d’approvisionnement.
Risque de fatigue des employés : La culture d’amélioration continue promue par le Lean Manufacturing peut, parfois, entraîner une pression accrue sur les employés pour produire toujours plus avec moins de ressources. Cela peut entraîner un risque de fatigue, de stress et de burn-out, et affecter la productivité et la qualité du travail.
Adaptabilité limitée à certains secteurs : Bien que le Lean Manufacturing ait été largement adopté dans de nombreux secteurs, il peut ne pas être aussi adapté à certaines industries où les processus de production sont intrinsèquement complexes ou où les exigences de qualité sont extrêmement élevées.
Malgré ces limites, le Lean Manufacturing reste une méthodologie puissante pour améliorer l’efficacité opérationnelle et la qualité des produits dans de nombreuses organisations. En comprenant ces limites et en les adressant de manière proactive, les entreprises peuvent maximiser les avantages du Lean tout en atténuant les risques potentiels.
Études de cas
Pour illustrer concrètement les résultats obtenus par certaines entreprises grâce à l’adoption du Lean Manufacturing, examinons quelques études de cas :
Toyota : Toyota est souvent considérée comme la pionnière du Lean Manufacturing. En mettant en œuvre des pratiques telles que le Juste-à-temps, le Kaizen et le Kanban, Toyota a réussi à réduire les coûts de production, à améliorer la qualité des produits et à accroître sa compétitivité sur le marché automobile mondial.
Amazon : Dans le domaine de la logistique et de la distribution, Amazon a mis en œuvre avec succès des pratiques Lean pour optimiser ses opérations. En utilisant des technologies telles que les robots de manutention et les algorithmes d’optimisation des itinéraires, Amazon a pu réduire les temps de traitement des commandes, améliorer la précision des stocks et offrir des délais de livraison plus rapides à ses clients.
Ces exemples montrent comment le Lean Manufacturing peut être appliqué avec succès dans une variété d’industries pour obtenir des résultats tangibles en termes d’efficacité opérationnelle, de qualité des produits et de satisfaction des clients.
Conclusion
Dans cet article, nous avons exploré en profondeur le concept du Lean Manufacturing, une méthodologie de gestion des processus de production qui vise à maximiser la valeur pour le client tout en minimisant le gaspillage. Nous avons examiné les principes fondamentaux du Lean, tels que le Juste-à-temps, le Kaizen et le Kanban, ainsi que les étapes pratiques de mise en œuvre dans une organisation.
Nous avons également examiné les nombreux avantages et bénéfices du Lean Manufacturing, notamment la réduction des coûts, l’amélioration de la qualité des produits et l’augmentation de la productivité. Enfin, nous avons souligné quelques études de cas illustrant les résultats obtenus par certaines entreprises ayant mis en œuvre avec succès le Lean Manufacturing.
Il est clair que le Lean Manufacturing offre un potentiel significatif pour les entreprises cherchant à améliorer leur efficacité opérationnelle et à rester compétitives sur le marché. En adoptant une approche systématique et en favorisant une culture d’amélioration continue, les entreprises peuvent réaliser des gains significatifs en termes de qualité, de productivité et de satisfaction des clients.
Dans un environnement industriel en constante évolution, le Lean Manufacturing reste un outil puissant pour transformer les processus de production et stimuler la croissance et la réussite à long terme. Il est temps pour les entreprises de saisir cette opportunité et de s’engager pleinement dans le voyage vers l’excellence opérationnelle grâce au Lean Manufacturing.